What is MIND4MACHINES?
MIND4MACHINESis a project funded through the INNOSUP-01 program of Horizon 2020 aimed at the digitalization of manufacturing companies and financed by the European Commission (Grant Agreement No. 101005711). The objective of the project is to provide the necessary support to manufacturing SMEs for the validation and subsequent adoption of the latest digital transformation technologies to achieve smarter, sustainable manufacturing with a more efficient use of resources, in line with the European Green Deal.
MIND4MACHINESis aimed at technology SMEs (including startups) that act as Industry 4.0 technology service providers, and manufacturing SMEs that act as industrial partners for technology adoption.
About AWAke
AWAke stands for “Augmenting Workers to Adapt to quick changes in production,” reflecting our value proposition: enhancing worker productivity through multimodal tools based on language technologies and AI.
AWAke is the name we give to the collaboration project between ANCORA and INDAERO within the framework of MIND4MACHINES. This project has allowed INDAERO to validate and adopt Ancora Worker Connect, incorporating the latest technological innovations in Natural Language Processing (NLP) and Artificial Intelligence(AI) from our product, as well as some improvements that emerged from the mutual collaboration between both companies during the project.
The solution deployed in AWAke frees workers from unnecessary details, reduces cognitive load, organizes actions to maximize productivity, and seamlessly checks coherence. Workers communicate in real-time with decision systems through voice and visual instructions that support quality inspection processes of manufactured components, accelerating the process within the context of Flexible Manufacturing Systems (FMS).
Challenges overcomed
Despite the high level of factory automation today, the impact of workers on the added value and quality of a manufactured product is a growing concern in many dynamic manufacturing contexts. Increased requirements for product customization, smaller production batch sizes, greater complexity in manufacturing certain products, and a shortage of skilled talent are just four ofthe many factors that make worker digitization a priority in Flexible Manufacturing Systems, which must manage highly variable manufacturing processes. The involved workers are not always as aware, skilled, and prepared for these changes as desired.
Our primary goal was to demonstrate that the use of AI technologies can assist workers by freeing them from much of the prior process training and increasing the irreliability and productivity in complex and variable tasks.
The challenge that AWAke has addressed is how to simplify all that increasing complexity in the dynamic process to provide simplicity to the worker when theprocess itself is unknown at the design phase.
With the evolution of Ancora Worker Connect (AWC), we have achieved an intelligent multimodal software tool that combines voice assistance with visual and tactile interfaces for manufacturing context management and validation in a relevant real manufacturing environment. This has allowed us to reach the level of maturity required to guide worker interactions through a flexible process that the worker won’t be familiar with in advance, effectively and error-free.
As a result, workers can perform dynamic quality checks at INDAERO factory workstations that produce components for the aerospace industry, with a substantial reduction in operation times, even for repetitive tasks.
The most innovative aspects of AWAke
AWC acts asan AI-powered cognitive exoskeleton for manufacturing workers, providing them with support, guidance, and assistance, reducing their cognitive load and stress, preventing human errors, enhancing performance, and avoiding or reducing unnecessary learning cycles and qualification needs in ever-changing procedures.
These benefits are supported by some of the most innovative elements of Ancora WorkerConnect:
- Dynamic multimodality, which combines natural language with visual and tactile interfaces within a unified user experience, optimizing/reorganizing access modes to enhance performance.
- Artificial intelligence capabilities to ensure the coherence of workers’ actions and reduce cognitive load and training time.
- Dynamic adaptation to the process and factory, achieved through the use of mobile terminals combined with our solution, specific devices for noisy environments, and configurable triggering mechanisms tailored to process requirements.
- Integration with the ERP/MES/MOM system for FMS. AWC has been able to address these challenges as an addition to INDAERO’s production management system.
Key Performance Indicators (KPIs)
One of the most relevant aspects of the collaboration with INDAERO in MIND4MACHINES AWAke is that we have been able to quantify the improvements introduced in the inspection processes where the solution has been implemented, some of which already had digital alternatives in place.
Among the various measurements conducted, three main indicators have been generated to exemplify the evolution in different phases of the analysed processes:
- KPI 1. Reduction in time to obtain instructions. It refers to the decrease in the time it takes to obtain the necessary information to a start quality control. The reduction achieved in this subprocess is 91.48%.
- KPI 2. Reduction in operator time performing measurements. It refers to the time during which the operator is effectively performing quality control measurements. The reduction achieved in this subprocess is 41.88%.
- KPI 3. Reduction in total process time. It refers to the time it takes for the operator to complete the entire process, from when they receive the Work Order (WO). The total reduction achieved in the process is 53.04%.
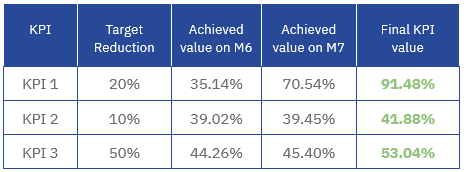
In conclusion, AWAke has enabled INDAERO to achieve a reduction of over 50% in the times of their quality processes, which has an immediate impact on the overall productivity of production lines and the bottom line.
User Value
In addition to the quantitative aspects and the impact on ROI and the client’s bottom line, Ancora always considers the positive impact on workers. The collaboration with the INDAERO team has also yielded relevant responses and conclusions in this regard.
Positive Effect of Acceleration in Preparatory Tasks
One of the key points for operators has been the reduction in time for tasks preceding the actual quality control. As reflected in KPI 1, a very significant reduction in time and work has been achieved, going from 7 minutes to less than 30 seconds.
This reduction has been highly rated by the workers, especially during those moments of the workday when fatigue becomes a determining factor. Combined with the cleanliness, organization, and freedom of movement in the workplace that digitization with Ancora Worker Connect provides, the solution positively influences performance, health preservation, and worker motivation.
Handoff
In line with preparatory tasks, the reduction in “handoff” time (process closure and transfer to the next station) has also been valued as a very positive aspect. This time practically disappears with Ancora Worker Connect, going from 2 and a half minutes to just 2 seconds.
Fewer Errors and More Assistance
The support provided to the operator during measurements by Ancora Worker Connect helps prevent human errors. These errors can become quite common towards the end of shifts or workdays due to fatigue.
Perception of Value in Digitized Processes
Another aspect identified in the collaboration has been the positive response from operators who already had digital tools to support the inspection process. Our expectation was lower for those positions, as they already had a digital foundation and experience using it. However, we emphasize greatly that a high value is perceived in our product by highly skilled workers using digital processes, which validates the competitiveness of our solution.
Supplier-Customer Collaboration as a Key Success Strategy
Throughout this entire project, INDAERO maintained a very close relationship with numerous virtual and physical meetings. Their support greatly facilitated communication, collaboration, and the results achieved by both parties. As a result of this support, two unforeseen improvements in user experience (UX) and hands-free triggering emerged, which were immediately incorporated into the product and played a key role in achieving the presented indicators. Once again, it is demonstrated that effective collaboration between technology suppliers and industrial customers is essential for addressing real challenges in factories.
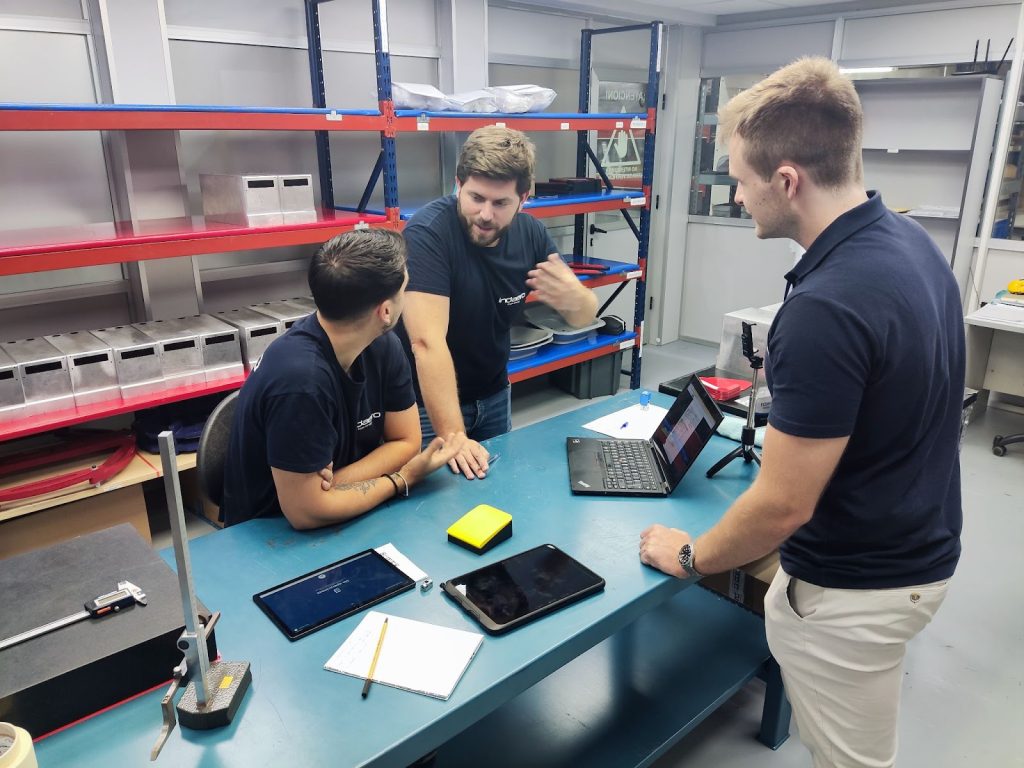